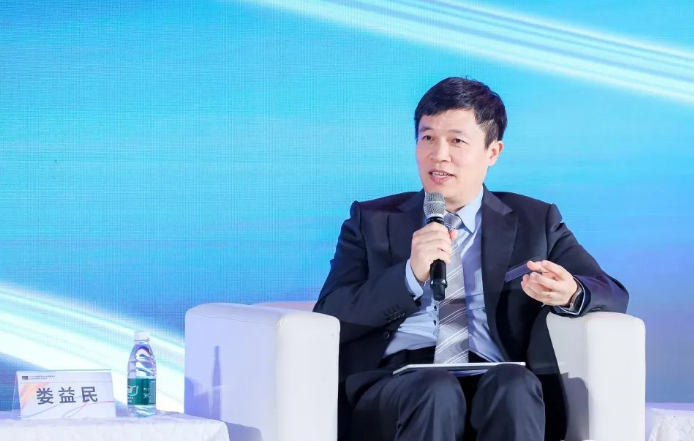
受訪人:遠(yuǎn)景能源高級(jí)副總裁、風(fēng)機(jī)產(chǎn)品線總裁婁益民
PART1:堅(jiān)持長(zhǎng)期主義精神
《風(fēng)能》:CWP2024上,大型化仍是整機(jī)企業(yè)技術(shù)與產(chǎn)品發(fā)展的主流方向之一,多數(shù)整機(jī)商推出了16MW級(jí)產(chǎn)品,甚至有的發(fā)布或下線了20~25MW級(jí)產(chǎn)品。與此同時(shí),業(yè)內(nèi)也有不少專家在呼吁關(guān)注大型化產(chǎn)品的可靠性問題,對(duì)此您怎么看?
婁益民:中國(guó)風(fēng)電整機(jī)產(chǎn)品的大型化確實(shí)比較快,當(dāng)產(chǎn)品更新的節(jié)奏過快時(shí),容易導(dǎo)致新技術(shù)的測(cè)試驗(yàn)證不夠充分。目前我國(guó)風(fēng)電機(jī)組單機(jī)容量已遠(yuǎn)超國(guó)際水平,遇到了不少全新的技術(shù)問題。如果一款產(chǎn)品有1000個(gè)與質(zhì)量相關(guān)的維度,即使對(duì)主要的100個(gè)維度進(jìn)行了測(cè)試驗(yàn)證,實(shí)際上還有900個(gè)甚至都不清楚在哪里。同時(shí),測(cè)試仿真模型僅在一定范圍內(nèi)有效,當(dāng)機(jī)組參數(shù)超出這個(gè)范圍,邏輯就會(huì)發(fā)生改變。當(dāng)風(fēng)電機(jī)組變得越來越大,我們對(duì)整機(jī)系統(tǒng)性的認(rèn)知會(huì)出現(xiàn)不少挑戰(zhàn)。因此目前機(jī)組進(jìn)一步大型化的基礎(chǔ)并不扎實(shí),還需要進(jìn)行大量測(cè)試驗(yàn)證工作。
《風(fēng)能》:您提到了大型化機(jī)組推出節(jié)奏過快,測(cè)試驗(yàn)證環(huán)節(jié)可能會(huì)有所欠缺,具體表現(xiàn)在哪些方面?
婁益民:在測(cè)試驗(yàn)證的范圍、時(shí)間、標(biāo)準(zhǔn)三個(gè)方面,都可以進(jìn)一步優(yōu)化提升。
首先是范圍有限。目前針對(duì)風(fēng)電機(jī)組這么大的整機(jī)系統(tǒng),我們關(guān)注的只是對(duì)幾個(gè)關(guān)鍵零部件做部分測(cè)試,主要特性可能沒問題,但很多其他的特性容易出問題。因?yàn)闄C(jī)組的主要特性是在以往問題中沉淀而來的,而現(xiàn)在出現(xiàn)的問題,是以往沒有出現(xiàn)過的。當(dāng)產(chǎn)品增大到一定程度,就要進(jìn)行全面測(cè)試,不能只針對(duì)某個(gè)方面。
其次是時(shí)間過短。歐美企業(yè)推出一款新品往往需要4-5年,我們可能只有4-5個(gè)月,這不符合科學(xué)邏輯。新產(chǎn)品從紙面轉(zhuǎn)化到實(shí)物,需要一定時(shí)間去研發(fā),再測(cè)試驗(yàn)證。一個(gè)傳動(dòng)鏈的測(cè)試驗(yàn)證,沒有8個(gè)月做不下來,當(dāng)它被搭載到整機(jī)上,還需要與其他部件協(xié)同的樣機(jī)測(cè)試,樣機(jī)測(cè)試也要分不同應(yīng)用場(chǎng)景,又需要一年時(shí)間,才能證明這個(gè)設(shè)備是基本可靠的。
再次是標(biāo)準(zhǔn)滯后。以往我國(guó)機(jī)組研發(fā)是依據(jù)國(guó)際標(biāo)準(zhǔn)進(jìn)行的,可以說是站在巨人的肩膀上。在單機(jī)容量2~5MW時(shí),還能采用現(xiàn)行的一些技術(shù)標(biāo)準(zhǔn),但到了15~20MW,國(guó)外也缺乏參考依據(jù)。近年來,國(guó)際權(quán)威標(biāo)準(zhǔn)中大多數(shù)失效處理方法,都是從中國(guó)經(jīng)驗(yàn)總結(jié)出來的,而我們還沒來得及在自己的標(biāo)準(zhǔn)規(guī)范中進(jìn)行沉淀。
《風(fēng)能》:前面提到的都是大型化發(fā)展面臨的挑戰(zhàn),以后我們?cè)撛鯓悠平膺@些挑戰(zhàn)?
婁益民:要堅(jiān)持長(zhǎng)期主義精神。不僅風(fēng)電,過去中國(guó)制造業(yè)有一個(gè)特點(diǎn),就是習(xí)慣于“趕抄”——趕著以最快的速度,將國(guó)際上的先進(jìn)技術(shù),轉(zhuǎn)化為自己的產(chǎn)品。在這個(gè)過程中,技術(shù)創(chuàng)新與研發(fā)的成本,很容易被忽視,所以中國(guó)企業(yè)在技術(shù)開發(fā)上投入的成本并不高。今天,中國(guó)風(fēng)電產(chǎn)業(yè)已經(jīng)發(fā)展到需要自己“創(chuàng)造”的時(shí)候,要求企業(yè)秉承長(zhǎng)期主義精神,做好自身技術(shù)積累工作。比如遠(yuǎn)景在進(jìn)行風(fēng)電零部件自研自制的過程中,就在充分認(rèn)知技術(shù)與產(chǎn)品的同時(shí),實(shí)現(xiàn)了整機(jī)價(jià)值鏈的垂直整合,創(chuàng)造了利潤(rùn)空間。這使得遠(yuǎn)景在今年有充足的底氣,不再進(jìn)行最低價(jià)投標(biāo)。相信通過遠(yuǎn)景與其他負(fù)責(zé)任的頭部整機(jī)企業(yè)共同努力,守住底線,這個(gè)行業(yè)會(huì)越來越好。
PART2:實(shí)現(xiàn)大部件與整機(jī)特性的貫通
《風(fēng)能》:有外界觀點(diǎn)認(rèn)為,遠(yuǎn)景能源搞零部件自研自制主要是為了節(jié)省制造成本。您上面提到了遠(yuǎn)景自研自制對(duì)于企業(yè)進(jìn)行產(chǎn)品研發(fā)也有好處,請(qǐng)介紹一下其中的邏輯。
婁益民:每一款風(fēng)電機(jī)組運(yùn)行在100多米的高空中,特性都是不一樣的,所以它的大部件不能太標(biāo)準(zhǔn)化。并且,當(dāng)機(jī)組發(fā)展到很大的時(shí)候,就更需要個(gè)性化。因?yàn)榇祟悘?fù)雜的系統(tǒng)太過標(biāo)準(zhǔn)化后,應(yīng)用能力會(huì)變差,可能出現(xiàn)各種各樣的問題。比如整機(jī)商在購入部件企業(yè)的標(biāo)準(zhǔn)化部件后,匹配在自身整機(jī)系統(tǒng)中不一定好用。遠(yuǎn)景在進(jìn)行大部件自研自制過程中,可以更明確地將大部件按照自身整機(jī)系統(tǒng)特性進(jìn)行設(shè)計(jì),從而實(shí)現(xiàn)大部件與整機(jī)特性的貫通,確保部件之間,部件與系統(tǒng)之間的完美匹配。
《風(fēng)能》:普遍觀點(diǎn)認(rèn)為,軸承與齒輪箱等傳動(dòng)系統(tǒng)關(guān)鍵零部件,只有專業(yè)公司能夠做得好,因?yàn)樗麄冋莆樟瞬牧稀⒐に?、設(shè)備、產(chǎn)能等。為什么遠(yuǎn)景能源也可以將軸承與齒輪箱的自研自制做好?
婁益民:以軸承為例。遠(yuǎn)景與主軸承供應(yīng)商的合作是從源頭開始,全程主導(dǎo)鋼材、熱處理、機(jī)加工、裝配、出廠檢驗(yàn)等全過程。在合作中,遠(yuǎn)景集成開發(fā)團(tuán)隊(duì)負(fù)責(zé)全鏈條的開發(fā)、評(píng)審、驗(yàn)證和放行,保證設(shè)備、工藝、人員等生產(chǎn)要素和過程管控滿足高質(zhì)量交付的要求。同時(shí),批量生產(chǎn)的質(zhì)量監(jiān)造會(huì)將每一個(gè)生產(chǎn)節(jié)點(diǎn)的數(shù)據(jù),反饋回遠(yuǎn)景質(zhì)量管理平臺(tái)進(jìn)行大數(shù)據(jù)分析,保證軸承制造過程能力的穩(wěn)定受控。
目前,遠(yuǎn)景齒輪箱工廠已進(jìn)一步擴(kuò)展為傳動(dòng)鏈工廠。近6000臺(tái)遠(yuǎn)景自研齒輪箱應(yīng)用于Model S、X、T、Y、Z五大風(fēng)電機(jī)組產(chǎn)品平臺(tái),實(shí)現(xiàn)非金屬雜質(zhì)零失效;近6000套遠(yuǎn)景自研主軸承應(yīng)用于14款風(fēng)電機(jī)組產(chǎn)品,至今零失效。
《風(fēng)能》:在上述自研自制軸承與齒輪箱的過程中,有沒有能夠體現(xiàn)工作細(xì)節(jié)的案例可供分享?
婁益民:為達(dá)到風(fēng)機(jī)30年可靠運(yùn)行的目標(biāo),主軸承產(chǎn)品必須具備極其強(qiáng)悍的耐載以及耐磨特性。實(shí)現(xiàn)這一特性,關(guān)鍵就是要保證高質(zhì)量的熱處理工藝水平。從某種程度上來說,主軸承產(chǎn)品的熱處理工藝質(zhì)量水平,決定著風(fēng)機(jī)軸承的疲勞耐久壽命水平。而這項(xiàng)工藝技術(shù)在國(guó)內(nèi)幾乎是空白。為突破這項(xiàng)工藝技術(shù),遠(yuǎn)景團(tuán)隊(duì)并肩戰(zhàn)斗在現(xiàn)場(chǎng)一線,協(xié)同科研院所及相應(yīng)試驗(yàn)資源,對(duì)整個(gè)工藝試驗(yàn)過程進(jìn)行反復(fù)迭代。從方案的策劃到實(shí)物的落地,一步步調(diào)整優(yōu)化設(shè)備、材料、工藝裝備、工藝參數(shù),期間團(tuán)隊(duì)成員全力保障設(shè)備連續(xù)運(yùn)轉(zhuǎn),短時(shí)間內(nèi)進(jìn)行了10多次不同工藝方案迭代,累計(jì)投入了80多件的試驗(yàn)材料、比對(duì)了上千張顯微金相圖片之后,最終找到了該工藝的最優(yōu)解??上驳氖?,該產(chǎn)品歷經(jīng)5輪次的大型臺(tái)架試驗(yàn),巍然不動(dòng)穩(wěn)如泰山,保證了自研主軸承在風(fēng)機(jī)應(yīng)用中的可靠性。本次風(fēng)展上,采用遠(yuǎn)景新型熱處理工藝的海陸平臺(tái)自研主軸承獲得了國(guó)際權(quán)威認(rèn)證機(jī)構(gòu)DNV頒發(fā)的IECRE認(rèn)證證書。
再舉一個(gè)齒輪箱的例子。針對(duì)風(fēng)電傳動(dòng)鏈大型化、集成化的發(fā)展趨勢(shì),以及客戶對(duì)高可靠性的需求,遠(yuǎn)景新開發(fā)樣機(jī)使用了超過400個(gè)高精度傳感器,實(shí)現(xiàn)了對(duì)傳動(dòng)鏈從外至內(nèi)包括溫度、壓力、應(yīng)變、間隙、振動(dòng)、載荷、系統(tǒng)形變等的全場(chǎng)感知。在測(cè)試驗(yàn)證時(shí)間和強(qiáng)度上也數(shù)倍于行業(yè)標(biāo)準(zhǔn):每個(gè)遠(yuǎn)景新開發(fā)機(jī)型都要進(jìn)行800~1000小時(shí)綜合測(cè)試,遠(yuǎn)超最新IEC標(biāo)準(zhǔn)要求的330小時(shí)。采用遠(yuǎn)景自研自制滑動(dòng)軸承齒輪箱的超百臺(tái)風(fēng)機(jī)運(yùn)行2年來零失效,證實(shí)了遠(yuǎn)景在測(cè)試驗(yàn)證環(huán)節(jié)不斷自我挑戰(zhàn)的價(jià)值和意義。
PART3:突破風(fēng)電成為主體能源的瓶頸
《風(fēng)能》:隨著“三北”地區(qū)風(fēng)電等新能源裝機(jī)規(guī)模不斷提升,依靠電力外送的方式進(jìn)行消納越來越難,構(gòu)建新型電力系統(tǒng)成為當(dāng)務(wù)之急。在您看來,推動(dòng)風(fēng)電占比進(jìn)一步提升,成為新型電力系統(tǒng)主體能源的瓶頸在哪?
婁益民:為將風(fēng)電等新能源在電網(wǎng)中占比從15%、20%提升至80%,需要通過新型電力系統(tǒng)來克服其波動(dòng)性問題,使其進(jìn)入到各行各業(yè)的負(fù)荷當(dāng)中。例如,未來微電網(wǎng)大多將以獨(dú)立網(wǎng)形式存在,其容量可能會(huì)很大,甚至達(dá)到1~10GW。所以國(guó)家在大力推動(dòng)構(gòu)網(wǎng)型風(fēng)電機(jī)組、構(gòu)網(wǎng)型光伏、構(gòu)網(wǎng)型儲(chǔ)能的發(fā)展。只有解決了構(gòu)網(wǎng)型設(shè)備的技術(shù)問題,并基于此建立起新型電力系統(tǒng),才能將清潔能源轉(zhuǎn)化成波動(dòng)性很小的綠電。只有當(dāng)新能源發(fā)電設(shè)備的離網(wǎng)或構(gòu)網(wǎng)能力瓶頸被打破,風(fēng)光的應(yīng)用場(chǎng)景就不會(huì)再被限制,也就不會(huì)出現(xiàn)棄風(fēng)棄光問題,新能源下一輪的大發(fā)展就會(huì)到來。
《風(fēng)能》:為建設(shè)好以風(fēng)電等為主體的新型電力系統(tǒng),除了做好構(gòu)網(wǎng)型與離網(wǎng)型新能源發(fā)電設(shè)備外,還要解決哪些挑戰(zhàn)?
婁益民:我們常說“源”隨“荷”動(dòng),實(shí)際上“荷”也要隨著“源”動(dòng),源荷要形成互動(dòng)。在這個(gè)過程中,一個(gè)非常重要的挑戰(zhàn)就是氣象大模型。要搞好風(fēng)電生產(chǎn),我們只有弄清楚超短期、短期、中期、長(zhǎng)期的風(fēng)能狀況,才能知道可生產(chǎn)多少電力、負(fù)荷如何去調(diào)配等等。例如用風(fēng)電去制造綠色氫氨醇,需要有一定穩(wěn)定性的電源才能進(jìn)行正常生產(chǎn)。所以最關(guān)鍵的是要實(shí)現(xiàn)從氣象模型到設(shè)備系統(tǒng)的智能化,然后再利用新型電力系統(tǒng)進(jìn)行總體控制,建設(shè)一個(gè)龐大的智能化系統(tǒng)。
來源:《風(fēng)能》雜志,文:趙靚
評(píng)論